Introduction:
From boat building to construction to aerospace manufacturing, the 3D printed strongback is transforming structural reinforcement and precision alignment across several sectors. Made historically from metal or wood, strongbacks provide solid frames to guarantee correct alignment and structural integrity during construction.
Strongbacks can now be custom-designed, lightweight, and reasonably priced as 3D printing technology develops; they are therefore available to both professional fabricators and do-it-yourselfers including engineers. This book will cover what a 3D printed strongback is, its advantages, materials utilized, optimal 3D printing techniques, troubleshooting advice, and often asked questions.
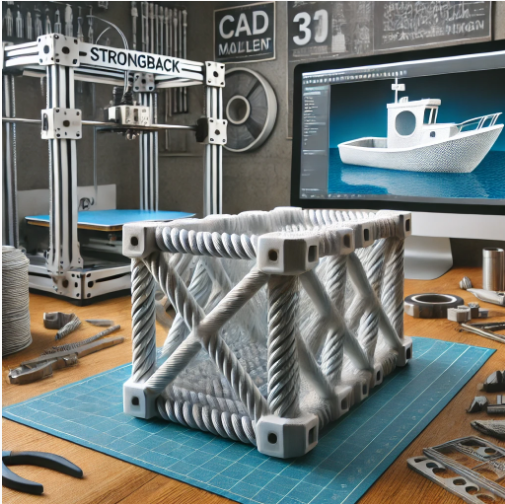
A 3D Printed Strongback Is:
In manufacturing, a strongback is a structural support system meant to keep alignment and strengthen structural integrity. Strongbacks are perfect for uses requiring accuracy since 3D printed versions may be tailored to particular forms, sizes, and weight tolerances.
Typical Applications for 3D Printed Strongbacks
- Boat Building: Guarantees alignment and hull symmetry.
- Construction and Architecture: Used in modular assembly, scaffolding, and concrete shaping.
- Aerospace and Automotive: Provides lightweight support systems for manufacturing aircraft and cars.
- Robotics and Engineering: Regular fixtures for industrial component assembly.
Advantages of a 3D Printed Strongback
1. Accuracy and Customizing
Customized strongback designs made possible by 3D printing meet exact project requirements, therefore guaranteeing improved alignment and support.
2. Strong & Lightweight
3D printed strongbacks can be lightweight but robust using cutting-edge materials like reinforced PETG or carbon-fiber-infused filaments.
3. Economical Manufacturing
Production of traditional strongbacks composed of metal or wood can be costly and time-consuming. 3D printing speeds up manufacture, cuts labor expenses, and removes waste.
4. Simple, Modular Assembly Technique
Interlocking components allow printed strongbacks to be built, therefore facilitating transportation and installation.
5. Fast Design Testing and Prototyping
Using 3D printing allows designers and engineers to iterate and test several strongback designs faster and easier.
Superior Materials for 3D Printing Strongbacks
1. PETG (Polyethylene Terephthalate Glycol)
✔ High strength and flexibility
✔ Heat and impact resistance
✔ Ideal for: Automobile and building applications
2. Carbon Fiber Reinforced PLA/PETG
✔ Lightweight yet remarkably strong
✔ Great stiffness and rigidity
✔ Ideal for: Robotics, aerospace, and boat building
3. ABS (Acrylonitrile Butadiene Styrene)
✔ Durable and impact-resistant
✔ Can be post-processed with acetone for a smooth finish
✔ Requires a heated bed for optimal printing
✔ Ideal for: Industrial engineering applications
4. Nylon
✔ Resistant to chemicals and moisture
✔ Superior toughness and elasticity
✔ Ideal for: Structural reinforcement of heavy-duty nature
Perfect 3D Print Settings for Strongbacks
1. Layer Height and Resolutions
- 0.2mm to 0.3mm for a balance between print speed and strength.
- 0.1mm for more finely detailed strongbacks.
2. Infill Density
- 50%–80% infill for high-strength applications.
- 30% infill for sturdy yet lightweight strongbacks.
3. Print Direction and Supports
- Lay the strongback flat on the print bed for best layer adhesion.
- Enable supports for overhangs greater than 45°.
4. Printing Speed and Cooling
- 40 to 60 mm/s for steady, robust layers.
- Turn off component cooling for ABS, but enable PLA and PETG.
5. Bed Adhesion
- Use a heated bed (50–80°C for PETG, 90°C for ABS, 100°C for Nylon).
- Apply PEI sheets or glue sticks to prevent warping.
Typical Problems and 3D Printed Strongbacks’ Troubleshooting Guide
1. Warping and Layer Separation
✅ Solution: Use a heated bed and an enclosure to maintain consistent temperatures.
2. Weak Structural Integrity
✅ Solution: Increase infill density and wall thickness to raise strength.
3. Bad Layer Adhesion
✅ Solution: Print at slower rates and slightly raise hot-end temperature.
4. Overhangs & Print Defects
✅ Solution: Enable supports for intricate designs and lower print speed for accuracy.
5. Nozzle Clogging with Fiber-Reinforced Filaments
✅ Solution: Use a hardened steel nozzle (0.6mm or more) to handle abrasive filaments.
READ MORE – 3D Printed Small Motor Holders: A Comprehensive Guide
FAQs:
1. Are heavy-duty uses for a 3D printed strongback possible?
Yes! Strongbacks printed in carbon-fiber PETG or Nylon can manage large stresses and loads.
2. How long does 3D printing a strongback take?
Print times depend on size and intricacy, ranging from 4 to 24 hours.
3. How best should a multi-part strongback be assembled?
Create overlapping joints and secure them with bolts, adhesives, or friction-fit mechanisms.
4. Could a 3D printed strongback replace a metal strongback?
Yes, for some applications. While metal is still superior for extreme loads, 3D printed strongbacks offer lightweight customization.
5. Where can I obtain 3D printable strongback designs?
You can find free STL files on:
- Thingiverse
- Printables
- GrabCAD
- Cults3D
Conclusion
Custom, sturdy, and reasonably priced strongbacks made possible by 3D printing now find application in many different sectors. Whether you’re working in boat building, construction, robotics, or aerospace, a 3D printed strongback provides precision, strength, and versatility.By choosing the correct materials, print settings, and reinforcement procedures, strongbacks that match traditional materials can be produced, saving money and improving efficiency.