Angle iron has long been a mainstay in manufacturing and construction for building strong frames and supports. Made historically from metals like steel or aluminum, angle iron offers the required strength and stability for many structural uses. But with 3D printing technology, the manufacturing of angle iron has changed dramatically. This paper explores the creative possibilities, advantages, and future of 3D-printed angle iron in custom production.
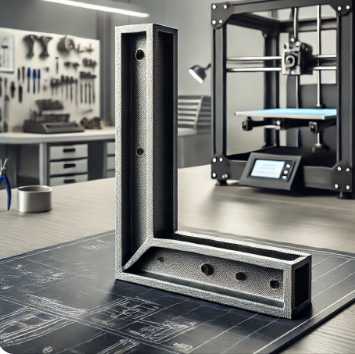
Comprehending 3D Angles Made of Iron
With its L-shaped cross-section, angle iron is important in supporting and reinforcing building and manufacturing projects. Cutting and welding metal pieces—a time-consuming and labor-intensive step in the conventional method of manufacturing angle iron—can be challenging. By building angle iron layer by layer from digital plans, 3D printing—also known as additive manufacturing—allows for unheard-of customizing and efficiency.
Benefits of 3D Printing in Angle Iron Fabrication
Flexibility in Customization and Design
3D printing lets designers produce angle iron with exact measurements fit for certain project specifications. Complicated geometries and custom designs that are difficult to realize with traditional approaches become possible, therefore promoting structural design innovation.
Quick production and prototyping
By accelerating the prototyping phase, 3D printing makes fast iterations and changes possible. This speedy development cycle shortens lead times and speeds up project completion.
Materials Cost Reduction and Efficiency
By employing just the required quantity of material to produce the component, additive manufacturing reduces material waste. This effectiveness not only helps to save resources but also lowers raw material expenses.
Demand Manufacturing on Demand
Angle iron components can be created as needed with 3D printing, therefore saving the requirement for extensive inventory. Custom projects or when replacements are needed right away benefit especially from this on-demand capacity.
3D Printed Angle Iron Construction and Architecture Uses
3D-printed angle iron finds use as structural supports, brackets, and connectors in building projects. Customizing every piece guarantees a precise fit, therefore strengthening the integrity and appearance of the construction.
3D-printed angle iron
Is used by manufacturers in assembly lines, equipment mounting, and machinery frames. 3D printing guarantees components satisfy exact criteria, so enhancing general operational effectiveness.
Do-it-yourself and household projects
Using 3D printing, hobbyists and do-it-yourselfers make angle irons for furniture, shelves, and bespoke fittings. This accessibility lets anyone work on projects using professionally graded components without specialist manufacturing skills.
Case Study: 3D Printing Helping to Overcome Supply Issues
An applications engineer building a custom apparatus with 80/20 aluminum extrusion provides a real-world illustration of 3D printed angle iron in use. Short on corner braces, the engineer looked to 3D printing to create the required internal components. The engineer effectively created the needed brackets in hours using an existing CAD model and a Markforged printer with Onyx material, at a material cost of only $2.70 per part. This method not only fixed the immediate supply problem but also proved the efficiency and economy of 3D printing in manufacturing useful hardware.
geometric tech.com
Design problems in the selection of 3D-printed angle iron materials
Choosing the right material will help to guarantee the durability and strength of the 3D-printed angle iron. Load-bearing applications demand materials like reinforced nylon composites (like Onyx), which balance printability with strength.
architectural integrity
Designers must take the load-bearing requirements of the angle iron into account and incorporate fillets and gussets to assist stress areas. Tools for structural optimization enable designs with the minimum possible materials yet maximum strength.
Print Orientation and Layer Attachment
The print orientation determines the mechanical features of the output. Aligning the print layers to run parallel to the direction of the applied load will help to increase tensile strength and reduce delaminating danger.
Difficulties and Future Possibilities
Although 3D printing has many benefits, manufacturing of bigger angle iron components may be affected by material restrictions and 3D printer size limitations. Still, developments in 3D printing technology keep solving problems. Larger-format printers and the arrival of new, stronger materials are opening doors for 3D-printed angle irons in many different sectors.
READ MORE – 3D Print Torx 25 Router Plate: A Complete DIY Guide
FAQs:
1. Would 3D printed angle iron have the same strength as conventional metal angle iron?
Although 3D printed angle iron produced from high-strength materials may not always match the strength of conventional metal angle iron, it can approach it. The particular use and load requirements determine the appropriateness.
2. Common 3D printing angle iron materials are what ones?
Often utilized are materials such as PLA, ABS, PETG, and reinforced nylon composites (e.g., Onyx). The choice relies on the necessary strength, adaptability, and application of environmental conditions.
3. Is 3D printing angle iron reasonably priced for big-scale projects?
Because of their economies of scale, conventional manufacturing techniques could be more affordable for big projects. On custom, low-volume, or intricate designs where conventional techniques would be cost-prohibitive, 3D printing is rather beneficial, nonetheless.
4. Three-dimensional printing of an angle iron component takes how long?
Size, intricacy, and selected print settings all affect the print time. Usually, small to medium-sized components can be produced in a few hours.
Conclusion:
3D printing offers unparalleled customization, efficiency, and flexibility that have revolutionized angle iron design and manufacture. While traditional metal angle iron is still the standard for heavy-duty structural usage, 3D-printed alternatives provide workable solutions for lightweight support systems, prototyping, and bespoke manufacturing.
From manufacturing and construction to do-it-yourself projects, additive manufacturing appeals to companies that can produce angle iron components on demand, eliminate material waste, and speed design iterations. As 3D printing technology advances, stronger materials, bigger build volumes, and maybe even more imaginative uses of 3D printed angle iron will become commonplace.