Introduction
3D-printed compact motor holders are essential in the realm of robotics, do-it-yourself electronics, and small engineering projects for ensuring and steadiness of motors. Whether you are creating a mechanical prototype, an automated system, or an RC car, a well-made motor holder guarantees stability, longevity, and accuracy. This book covers what you need to know about 3D printing motor holders, including the best materials, design issues, printing settings, and post-processing methods. We will also address the most often asked questions on 3D printed motor mounts to enable you to maximize your prints for lifetime and efficiency.
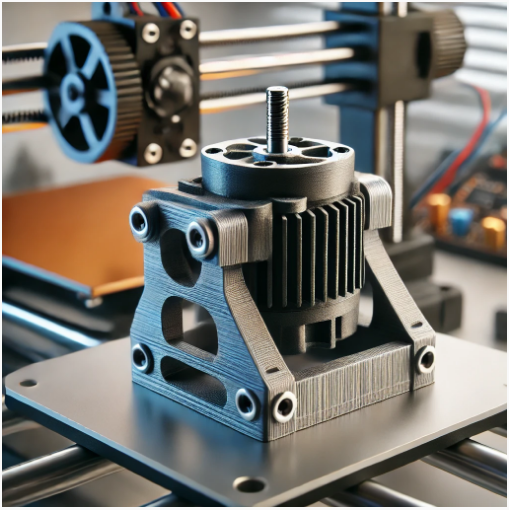
Why Might One Use a 3D Printed Little Motor Holder?
Many advantages abound from a 3D printed motor holder over conventional store-bought or handcrafted mounts:
- Customizing the design will help you to match your particular motor size and project needs.
- Cost-effectiveness: 3D printing lets you make robust motor mounts for a small fraction of the cost of commercial options.
- Strong and Lightweight: Well-crafted 3D printed mounts offer strong support free from needless weight.
- Quick replacement component printing instead of waiting for shipment will help with fast production.
- Use several materials, forms, and fastening methods to fit different motor kinds.
Top Three-Dimensional Printing Materials for Motor Holders
A 3D-printed motor mount’s performance and lifetime depend much on the material chosen. These are the top filament options:
1. Polylactic Acid (PLA)
- Easy printing, good dimensional accuracy, and reasonable price are benefits.
- Brittle under stress and less heat-resistant are drawbacks.
- For non-load-bearing or prototype motor holders.
2. PETG (Glycol-Modified Polyethylene Terephthalate)
- Strong, somewhat heat-resistant, and impact-resistant.
- Cons: Prints are somewhat more difficult than PLA.
- Best for medium-load motor holders needing durability and robustness.
3. ABS (Acrylonitrile Butadiene Styrene)
- High impact resistance, robustness, and heat resistance define pros.
- Cons: Calls for correct ventilation and a heated bed.
- For motor mounts in high-heat surroundings or with mechanical stress exposure.
4. Nylon
- Strong, flexible, and wear-resistant qualities abound.
- Cons: Calls for high-temperature settings and difficult printing.
- Best for high-performance motors and heavy-duty uses.
5. TPU (Thermoplastic Polyurethane)
- Flexible, shock-absorbing, vibration-resistant.
- Cons: Little structural stiffness.
- Ideal for applications where shock loads or vibrations affect the motor.
Design Factors for 3D Printed Motor Holders
Design a 3D printable motor holder with thought for the following:
1. Motor Compatibility for Size
Make that the mount’s attachment points, height, and diameter match your motor type—that is, NEMA 17 stepper motor, DC motor, or brushless motor.
2. Mounting and Fastening Choices
- Screw holes let you securely fasten something to a surface or frame.
- Perfect for tool-free assembly are clamp or Snap-Fit designs.
- Strengthen fastening points and stop peeling using embedded nut slots.
3. Heat Dissipation
If the engine produces heat, think about designs including heat sinks or ventilation slots to help with cooling.
4. Resistance to Vibration
Absorb vibrations and lower mechanical strain with flexible TPU components or strengthened walls.
5. Optimize Printability
- Limit overhangs to decrease the demand for support.
- Strengthen weak places with chamfers and fillets.
- Make sure the component faces ideal layer adhesion.
Setting 3D Printing for Motor Holders
Use these print settings to get a sturdy and exact motor holder:
- Layer Height: Durability calls for 0.2mm; high-detail mounting calls for 0.1mm.
- Infill Density: 40–100% depending on strength needs.
- Wall Thickness: For improved structural stability, 2–4mm.
- Print Speed: Best strength at 40 to 60mm/s.
- Supports: Use only where required to cut post-processing work.
- Bed Adhesion: For bigger pieces, a raft or brim is advised to prevent the warping of the bed.
Techniques of Post-Processing
Some post-processing actions after printing could improve the usability and lifetime of your motor mount:
1. Smoothing and Sanding
- Smooth edges using fine-grit sandpaper.
- For ABS printing, give acetone vapor smoothing some thought.
2. Drilling or Threading
- If necessary, create exact screws’ holes.
- Use stronger mounting points using threaded inserts.
3. Coating and Painting
- Strengthen the part and guard against wear by applying epoxy or a clear coat.
4. Heat Treatment (Annealing)
- Annealing PLA or PETG parts at controlled temperatures will help to increase heat resistance and strength.
READ MORE – 3D Printed Simple Castle: A Step-by-Step Guide to Creating Your Own Miniature Fortress
FAQs:
1. Can a 3D Printed Motor Holder Manage high-torque motors?
Indeed, you also need solid materials like ABS, PETG, or nylon and reinforced designs with correct mounting locations.
2. How May Motor Vibration Damage a 3D Printed Holder?
In high-stress regions, reinforce walls or absorb vibrations using TPU or rubber mounts.
3. For Motor Holders Needing Heat Resistance, Which Filament Is Best?
Under the heat, ABS, nylon, and PETG shine the most. Steer clear of PLA for high-temperature producing motors.
4. How Might I Affix a 3D Printed Motor Holder to My Project?
The design and application will dictate whether you utilize screws, nuts, zip ties, or adhesives.
5. Where May I Get STL Files for Motor Holders?
Free and premium motor mount STL files are offered by websites such as Thingiverse, MyMiniFactory, and Cults3D.
Conclusion
Prototyping, robotics, and do-it-yourself electronics all depend on a 3D-printed tiny motor holder. Choosing the correct material, design, and print settings will help you to provide a sturdy, custom-fit, reasonably priced solution for small motor security in different projects.
Proper post-processing and vibration control methods allow a 3D printed motor mount to compete commercially in durability and precision. A well-designed 3D-printed motor holder can greatly improve performance and dependability whether your project involves an RC car, a CNC machine, or automation.